Evolution of injection-blowing technologies
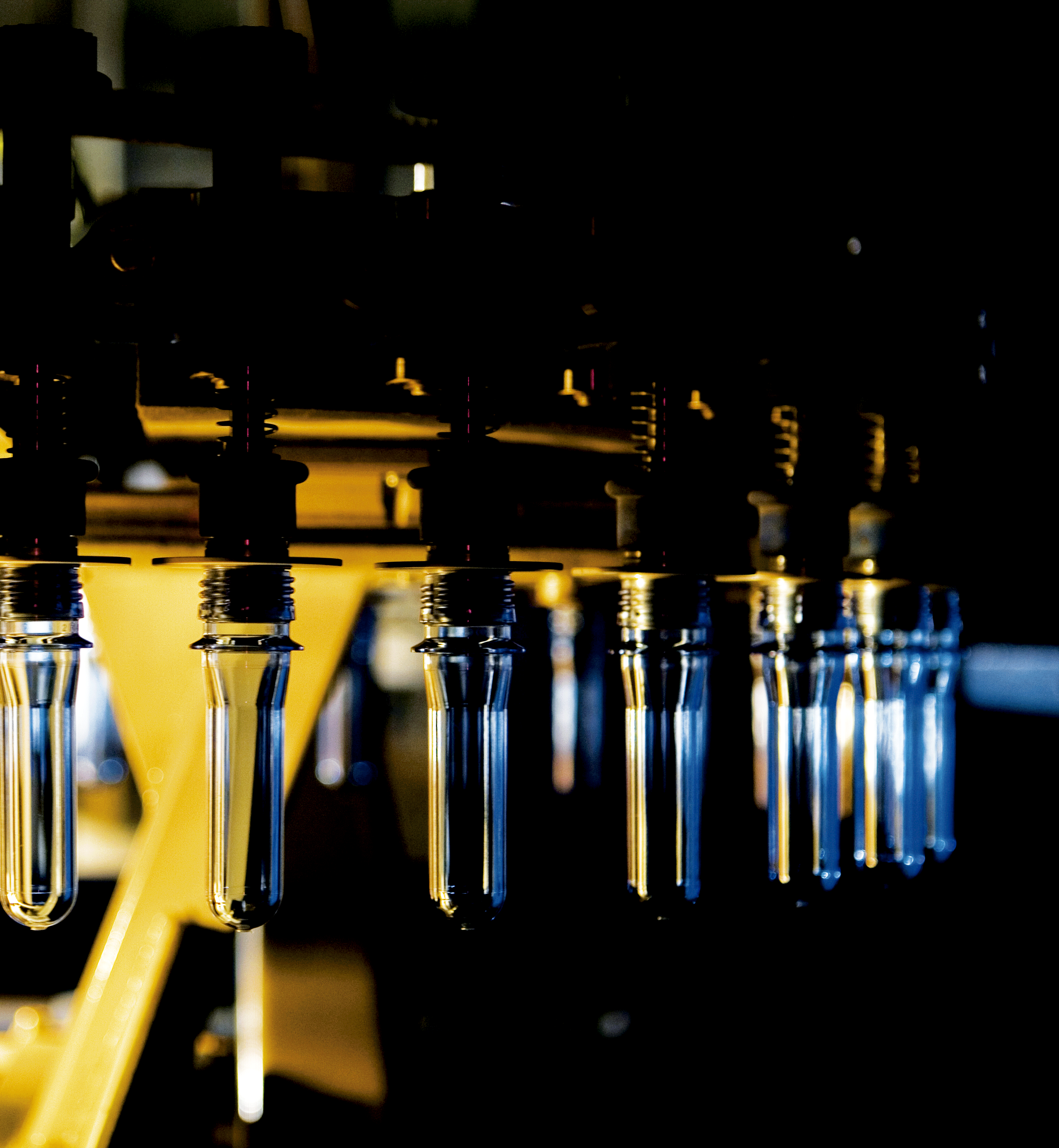
The injection-blowing process combines the injection moulding process, followed by a blowing moulding. This process can be divided in two phases differentiated: the injection phase, where a provisional piece is produced (called preform), and a blowing phase, where the product with the searched form is obtained. After that, there is the post-processing operation to get the final product completely finished, such as the cut, labeling and decorating operations, etc.
Injection Blow Moulding
We can find different variants of this process in the market. On the one hand, there is the basic injection- blowing process (IBM, Injection Blow Moulding), where the injected preform is blown before it is cool under its vitreous transaction temperature, when the material is still malleable. This process is normally divided into several stops, in where the preform passes and the necessary operations are carried out. It is normal that three phases are configured, but even more, it is being imposed a fourth phase with the intention of optimizing the process. Concretely, this variant will be detailed below, since it is the most used.
Reheat Blow Moulding
A modification of this basic process is known as Reheat Blow Moulding (RBM). In this case, the two phases of the process are physically separated, since there is a complete injection process of the preform, and a blowing process is carried out separately. They can be stocked up to be blown when it is necessary, or can even being transported to other companies (they are normally bottling and heat them and conform the definitive package). This technique is practically used for manufacturing PET bottles.
At this point and due to the newness which were pretended to be got (shapes, dimensions and new materials), there was a technical limitation when these packages were blown, since the materials were not as deformable as the required to be adapted to the form or dimensions of the bottle; it could be caused by the material’s properties or by its geometry.
Injection Stretch Blow Moulding
To amend this limitation, a stretching system of the preform was included, while it was also blown. Like this, the material can be deformed and reach all the mold’s points. With this system, slimmer materials with materials with higher viscosities than the materials used until now have been manufactured, without increasing the processing temperatures. This variant is known as Injection Stretch Blow Moulding (ISBM). It can be carried out in one phase, so it is practically equal to the Injection Blow Moulding (IBM) variant, but with stretching assistance when the preform is blown; it can be also carried out in two phases, which is practically equal to the Reheat Blow Moulding process (RBM).