Analysis of PET bottles intended for beer packaging
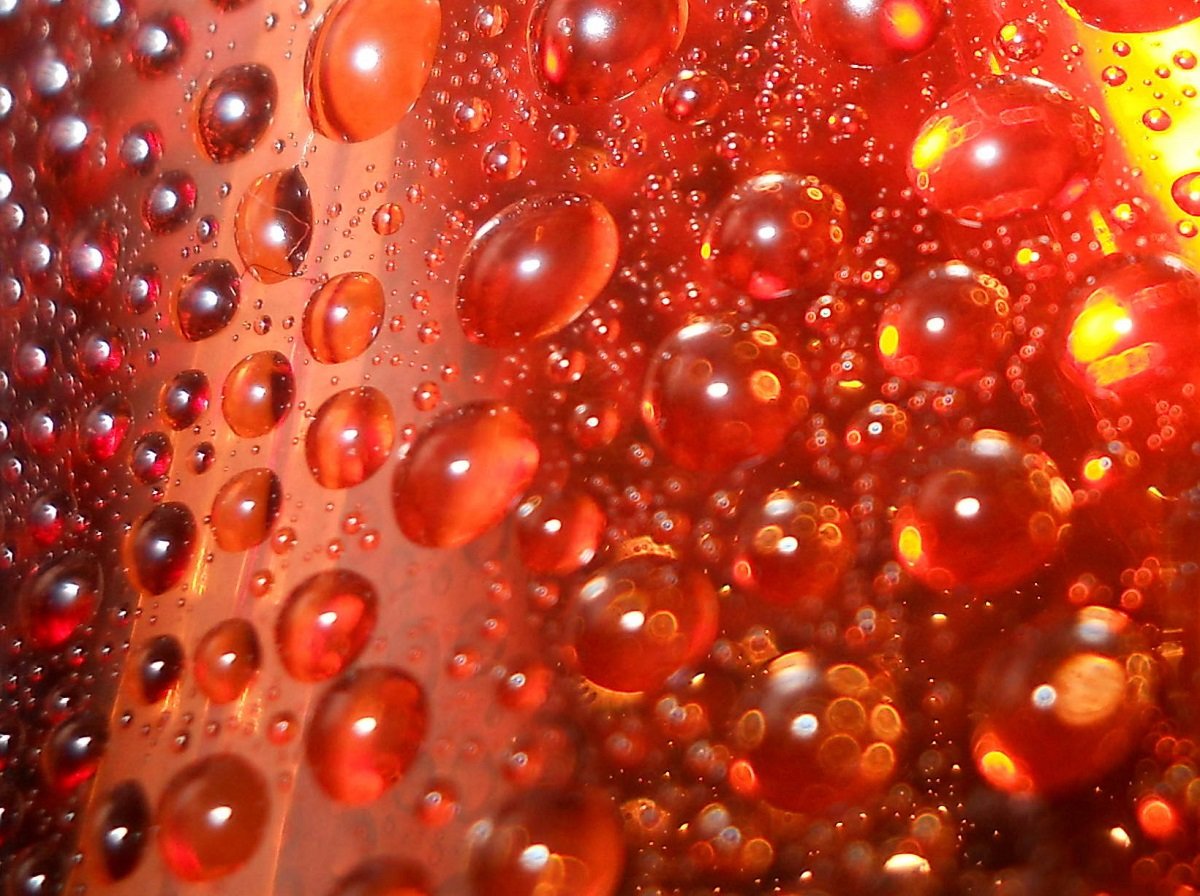
Since the implementation of the injection-blowing processes, polyethylene terephthalate (PET) bottles are present in a wide variety of packages in different sectors, such as the food, cosmetics and pharmaceutical industries. The packaging of liquid food is one of the applications in which this process and material have found a niche, thus displacing the materials previously used. Water, soft drinks, beer, wine, oil, are currently packaged in PET bottles. Each liquid has its particularities in terms of optimum conservation and it is affected differently by the exposure to oxygen, light and temperature. For beer packaging, it is important that PET bottles do not allow the gas transfer between the outside and the inside of the package, in particular oxygen and carbon dioxide. Although PET has good barrier properties, for beer packaging, they must be improved by increasing the base barrier factor of the material. For that purpose, different strategies are used:
- Use of Oxygen Scavengers added as PET additives (monolayer bottles).
- Mixture of barrier materials with PET (monolayer bottles).
- Use of polymeric layers with barrier materials (multilayer bottles).
- Use of coatings (monolayer bottles with 10-100nm coating).
In recent years, a change towards the manufacturing of PET bottles with coatings inside them has taken place thanks to the development of the Plasma Enhanced Chemical Vapour Deposition (CVD) techniques. These coatings, with thicknesses between 10 and 100nm, confer the PET package for beer an improvement in its oxygen and carbon dioxide barrier properties, maintaining the flexibility of the packaging, the transparency, the stability against packaged beverages and the recyclability of the packaging. Coatings applied by Plasma Enhanced CVD techniques are of two types: Diamond-like Carbon (DLC) and thin films made of silicate oxides (SiOx).
The detection of this type of coatings in PET bottles for beer packaging has some problems if we use the common and fast techniques for the analysis of plastics. As common techniques for the analysis of the composition of PET bottles we can mention the Fourier transform infrared spectroscopy (FTIR) and the differential scanning calorimetry (DSC). In this article, two PET bottles for beer packaging used by different bottlers have been analysed by FTIR and DSC and no differences have been found. By means of FTIR infrared spectrums of the external and internal surfaces of both bottles were performed by using attenuated total reflectance (ATR) techniques on diamond glass.
In these cases, only the presence of PET is detected and no difference can be established between both packages.
By means of DSC, thermograms have been obtained after eliminating the thermal history of the bottles, but no differences have been obtained in the thermal transitions detected for both samples.
Because of the similarity of both materials we can suspect techniques have been used to improve barrier properties different to mixture and multilayer’s ones and probably both bottles are examples with inner coating or with ‘oxygen scavengers’.
To determine if there is any type of coating on the inner side of the bottles the scanning electron microscopy (SEM) and the energy dispersive x-ray spectroscopy (EDX) have been used. In order to analyse the samples, a coating with gold (sputter coating) on its inner surface has been used. In this case and for both bottles, the presence of silicates on the inner surface has been detected, which means that the technology used to increase the barrier properties was the Plasma Enhanced CVD to coat with SiOx.