Insulating plastics: polyurethanes
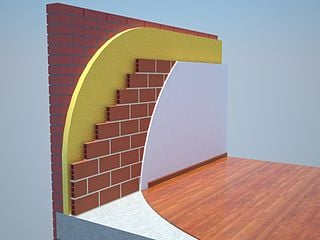
Since 1937 Otto Bayer followed the first synthesis of the polyurethane of which this material has become a daily element in our lives. We can find polyurethane in different products; in the medical sector as medical device housing, in the transport sector as an integrated part of vehicles, in devices for sport, in construction elements as an insulated thermal and acoustic element, in impermeable coverings and on road surfaces, among many other uses.
Polyurethane obtained by its reaction to two components; one component that contains two less functional alcohol groups- functional group -OH, called polyol, and a component containing at least two -NCO functional groups, called polyisocyanate . Of these two components, several additives must be added which will determine, together with the characteristics of the polyol and the polyisocyanate used, the final properties of our product.
Types of polyurethanes
Polyurethane can be thermostable or thermoplastic. We can classify thermostable polyurethanes in:
- Flexible polyurethane foams
- Rigid polyurethane foams
- RIM whole skin and polyurethane foams
- Bio-based Polyurethanes
- Without forgetting paints, varnishes, and coatings in general (pavements, waterproofing membranes) on a polyurethane basis
Flexible polyurethane foams
Flexible polyurethane foams have a limit of resistance in the presence of load application, its internal structure is open cell, permeable in air and has an elastic behaviour in the presence of deformation. The flexible polyurethane foams above all are used in the mattresses, upholstery, and automotive industry.
Rigid polyurethane foams
Comparing with other insulated materials, rigid polyurethane foams present one of the lowest values of thermal conductivity. In addition, it is important to emphasise the soundproofing properties it demonstrates. We can find numerous applications of this type of polyurethane as insulated in refrigerators and freezers, industrial plants (tanks, pipes, shipbuilding, construction sector…) and other soundproofing and thermal insulation projects in construction and automotive.
PUR insulation can be injected into wall cavities to create an energy efficient barrier. The foam is able to reach small spaces to create an air-tight seal. According to the Insulation Manufacturer Association, PUR provides “the best thermal performance of all practical full cavity insulants.”
PUR foam can be continuously sprayed onto any type of surface. It is generally less expensive than other materials, making it ideal for renovations.
RIM integral skin and polyurethane foams
If we carry out a careful balance between all the reactions that occur during formation of polyurethane foams, adjusting the mould temperature, the type of quantity of foaming agent, and the packing of cells, we can follow the formation of moulded pieces with a cellular nucleus structure covered by an exterior skin made from the same material, this type of material is called “integral skin” (DIN 7726)
The pieces carried out from the integral polyurethane foam presents a high reactivity because it has been necessary for the introduction of new transformation processes that allow the dossing and the mix of a great variety of primary substances in a brief period of time. The advancement in these processing technologies led us to what is known today as the RIM (Reaction Injection Moulding) process.
RIM integral skin and polyurethane foams offer us advantages in the construction and design of moulds due to the range of mechanical properties that they offer us and the increased variety of surface finish variety and density distribution. Its application in the automotive industry is of special relevance due to it using pieces of integral skin it is possible to decrease the weight of parts satisfying the mechanical properties required for it fundamentally reducing the weight of the vehicle (thereby reducing CO2 emissions) and maintaining the security parameters. Other areas of application in these types of products are sports objects, furniture and housings of electronic devices or medical.
Bio-based Polyurethanes
The demand for petroleum monomers to synthetize polymers has increased a lot, despite of the decrease and the price fluctuation of fossil resources. It is in this context that the development of bio-based and renewable products began to appear in the polymer sector, in particular for the development of biobased polyurethane. The polyurethane as explained previously are obtained by the reaction between polyol polyester or polyether and isocyanate. For the development of biobased polyurethane, it can be possible to substitute one of the components or both. The polyol that has functional hydroxyl groups can be obtained from biomass resources by using functionalized vegetables oils, lignin derivatives, cellulose derivatives but also agro-industrial waste. The isocyanate also can be obtained from the biomass by using fatty acid, lignin derivatives but also biobased amino acids. The polyurethanes developed will have a determine percentage of biobased contents which will have a positive impact on the carbon footprint.
The biobased polyurethanes can be used for different kinds of application such as flexible and rigid foams, elastomers but also coatings but also as polymeric matrix for composites depending on the biomass resources used for the synthesis of the polymers. The biobased polyurethanes can be used in many industrial sectors in addition to the construction sector.
Non-isocyanate Polyurethanes
All of them can be used for instance to produce NIPUs (non-isocyanate polyurethanes) according to the new horizons which are related with avoid isocyanate using due to its toxicological issues (REACH nº1907/2006). Such an approach eliminates hazardous chemical compounds from the synthesis and leads to the fabrication of polymeric materials with unique and tunable properties.
Non-isocyanate polyurethane (NIPU) or, more precisely, polyhydroxyurethanes (PHUs), is mainly derived from the reaction betweencyclic carbonate and polyfunctional amines. However, more recently, numerous strategies have come to the fore seeking to utilize the abovementioned renewable resources for the synthesis of NIPUs to meet the prerequisites of green chemistry and to pave way for their applications in the PU industry. Possible applications include coating, adhesives, foams, sealants, and elastomers. A related solution is hybrid non-isocyanate polyurethane (HNIPU) which is one of many ways to address the problem of using substances that are harmful to the environment because it can be developed through a solvent-free and catalyst-free synthesis is an eco-friendly way to obtain desired materials without stress on product purification and waste treatment. Although the material is still under research, it has applications in coatings, interior and exterior paints, flooring, and packaging. Hybrid Coating Technologies has developed Hybrid Non-Isocyanate Polyurethane (HNIPU) through patented technology.
If you need advice on polyurethanes or Bio-based Polyurethanes, get in touch with us.